Fence Installation Charlotte NC is a complex job that requires special tools. Consult your local Handyman to determine the specific materials required and to understand the local rules & regulations about fencing height, material type, and placement.
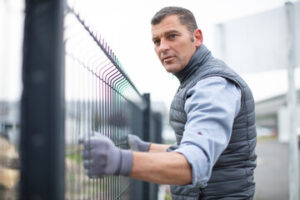
Setting posts is an essential first step, laying the foundation for stability and alignment throughout the construction process. Using a level is important to guarantee posts are perfectly placed and level.
The first step in fence installation involves putting the foundational posts in place. This will help ensure a strong, stable structure that can withstand the pressure of horizontal rails and vertical planks. Posts are typically set in concrete footings, which can provide an extra layer of strength and protection against frost heaving. The location of the post hole should be carefully assessed to avoid pipes or other obstructions and also to determine the appropriate depth based on local climate conditions and soil analysis.
Once the site has been cleared and the ground prepared, it’s time to dig the holes for the fence posts. This is an important step because the location of each post will determine how much tension is placed on that section of the fence. For example, a corner post will be subjected to the most strain because it will support the fencing in two different directions. These posts need to be set at a deep enough depth to resist shifting over the course of freeze-thaw cycles.
Depending on the type of fence you are installing, posts can be set in concrete or in gravel footings. If the latter option is chosen, it’s often recommended to add a bit of concrete mix to the bottom of the hole and use a tamping tool to pack it down firmly. This will prevent the post from settling and weakening over time.
Using a string line is essential for ensuring that the posts are all straight, even and properly spaced as planned. Some fence installers may choose to invest in lasers or other expensive tools for this purpose, but a simple string and a level can serve just as well in many cases. Having a straight-looking fence is important because it will not only provide a more attractive aesthetic, but it will also minimize potential issues down the road caused by an unbalanced or unstable structure. It’s not uncommon for homeowners to select cedar posts for their fences, as these materials are naturally resistant to bugs and rot. However, if the fence is to be used in a garden area it may be a good idea to consider metal posts because they don’t leach chemicals into the surrounding soil.
Horizontal Rails
Fence posts anchor the structure, but horizontal rails add strength and support. Rather than a vertical up-and-down appearance, horizontal fences have rails at the top and bottom that allow for a more contemporary look with the added benefit of preventing sagging over time.
Adding a top and bottom rail also makes your fence safer and more attractive, making it more difficult for kids and pets to climb. The rails can be either solid or woven depending on your design. For example, basket-weave fencing has open spaces that admit breezes but limit visibility while a closed louvered fence provides privacy and interesting shadow lines.
For a standard wood fence, install the top and bottom rails at least six inches above ground level to keep them away from moisture that can cause decay and to make it easier to trim grass or roots. For a component fence, use a mason’s line to mark where to install the rails. When the concrete has cured, install the rails (also called stringers). If your site is sloped, you’ll need to cut stringers shorter to follow the ground contour.
Start by fastening a 1 x 3 center board in each bay between the rails. This will provide stability and keep the woven fence boards from shifting or warping. If you’re installing a louvered fence, alternate the placement of the louvers (also known as louver stops) on the flat rail frame to create an open or closed style.
Fit the top and bottom rails onto the crossbar or fence post. Using a marking tool, denote the rail placement ensuring that the pre-punched swivel holes are directly opposite one another (Figure 2). Then, build the rail frames, tack on the infill and then toenail the infill down. If you’re installing a butted or through rail fence, tack on spacers between the butted or through rails and alternate with butted or through rails every other board. This will limit the side-to-side pressure on the fence boards and prevent sagging.
Vertical Planks
Once the foundational posts are in place, the fence begins to take shape as rails and panels or pickets are affixed. It’s at this stage that attention to detail is crucial, as these aspects define not only the functional strength of the fence but also its overall appearance. Taking the time to ensure that each plank is properly leveled and attached to the rails will result in a smooth, consistent look throughout your fence installation.
While a wood fence is an excellent way to secure property boundaries and create privacy, it’s important to know the proper construction techniques. This includes examining property titles to determine whether the proposed fence abuts any easements and observing any zoning restrictions regarding fencing setbacks from your home’s exterior. You should also be sure to discuss the fence’s placement with your neighbor to ensure that you’re not building on their land.
A reputable and trustworthy fence contractor will provide clear, detailed estimates outlining the costs involved in your project as well as a projected timeline for completion. In addition, they’ll be able to answer any questions or concerns you might have about your fence installation.
The best way to determine if a fence company is a good fit for your needs is to contact them for a free consultation. A good contractor will be happy to discuss your project with you and help you come up with a design that suits your space.
If you’re interested in becoming a fence company manager or owner, consider attending a training course offered by AFA. These courses offer valuable information that can help you manage your team, increase sales and profits, and build lasting customer relationships.
A fence is a significant investment, and regular inspections are essential to maintaining its structural integrity and aesthetic appeal. By identifying and addressing minor issues as soon as they arise, you can save yourself from costly repairs down the road. Our annual inspections typically include checking for loose nails, damaged planks, and any signs of rot to ensure that your fence continues to perform at its best.
Attaching Panels
When building a fence from scratch, it’s important to use quality lumber that has been treated with preservatives or a sealant to protect it from the elements. It’s also a good idea to stain or paint the wood once it’s dry. Staining helps preserve the timber and makes it easier to clean, which reduces the risk of mold growth and bacteria.
One way to save time during the fence installation process is to erect fence panels, which are pre-assembled and ready for you to install. When doing this, it’s crucial that you follow all the instructions and use all the necessary tools.
When installing a wooden fence panel, start by securing the bottom of the panel to the ground using galvanised clout nails or fence clips. Then, raise the panel 50 to 75mm above the ground by attaching it to temporary bricks. This will help prevent the fence from rotting from the bottom up. When it comes to securing the rest of the panel to the batten framing, use a spirit level to make sure it’s perfectly horizontal before hammering in the nails.
Once the posts are erected and the fence panels are in place, you’ll need to add blocker boards underneath the panel to stop the soil from sagging. This will ensure the fence remains strong and stable over a long period of time. For maximum protection against rot, it’s a good idea to use pressure-treated wood for the blocker board material.
While working on your fence, always be aware of any underground utilities that may be in the vicinity. If in doubt, it’s best to hire a professional service that can mark out the area of your proposed fencing site with a taut string and use a cable avoidance tool to dig the post holes without damaging pipes or cables.
If you decide to use fence panels for your fence, you’ll need to plan how many of each type you’ll require and take into account gates. Once you’ve done that, dig the post holes according to the length of your fence and allow plenty of room for the gate. You can speed up the process by using a post hole digger, which makes the job much faster.